平面研削盤
平面研削盤は加工物の平面を精密加工するもので 加工物の形状,大きさ,精度およびロットの大きさによって いろいろな平面研割方式がある。
その方式は図2に示すように大きく分けて,砥石軸が平行か, 垂直かまた加工物を取付けるテーブルが角テーブル往復形か あるい は円テーブル回転形かによって定まる。
そのほか. 2つの砥石で加工物の両面を同時に研削する両頭形もある。
平面研削盤の各部の名称
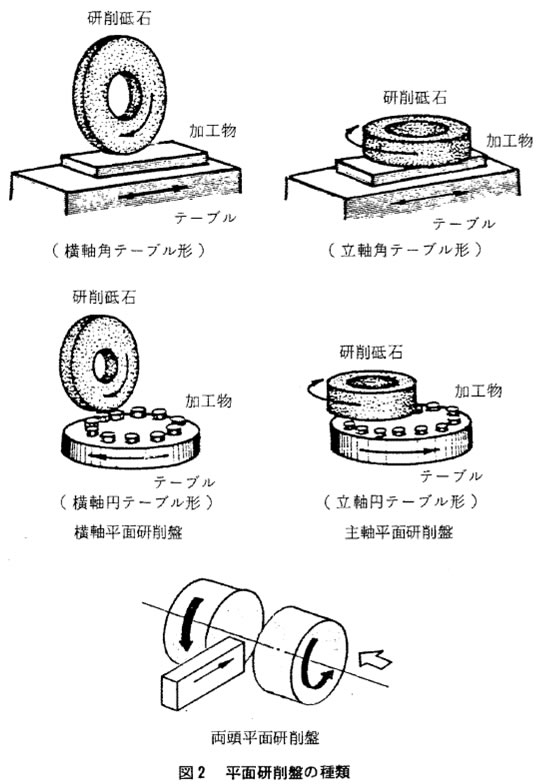
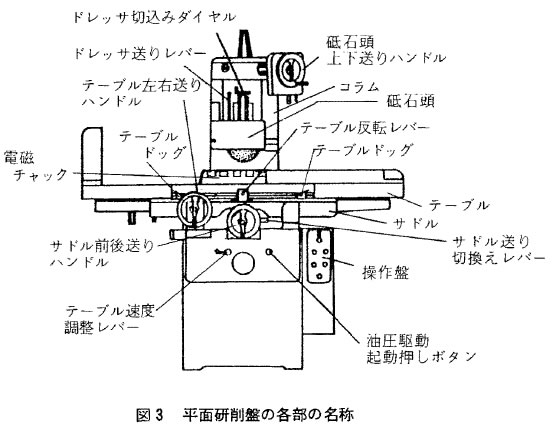
平面研削盤の各部名称 横軸角テープル形平面研削盤ににつ いて示す。
ベッドの上に前後に移動するサドルがあり、その上に左右に動くテーブルがある。 テーブルの上に電磁チャックがのっている。
砥石の切り込みは、コラムに沿って砥石頭が動くことによって行われる。
平面研削盤を手動操作するためのハンドルとして,サドル前後送りハ ンドル,テーブル左右送りハンドル, 砥石頭上下送りハンドル(砥石切込みハ ンドル)および、ドレッサ切り込みダイヤノレなどがある。
電磁チャック面は,研削盤に付いている状態で研削(セルフラインディング)してあるので前後送りのための摺動面及び左右送りのための摺動面のそれぞれに平行になっている。
砥石の使い方によって作業方式をいくつかに分類することができる。
トラバース研削とプランジ研削である。
図4に示すように, トラバース研削とは,テーブルを左右に動かしつつ,サドルを前後に送って加工物の平面を削る方式である。
トラバ-ス研削は,加工物を前後,左右に送って研削するため,精度のよい平面が得られる。
一方,サドルを前後に送らないで,左右送りだけの場合をプランジ研削という。 図5はフランジ研削方式で,総形研削(プロファイル研削)の例である。
プランジ研削は,砥石作動面全面が同じ切込みになるため能率がよい。 図6のように研削砥石の外周面を使う円周研削と図7のように研削砥石の端面を使う正面研削に分類することができる。
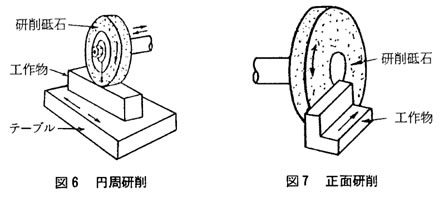
正面研削は,砥石強度の弱い方向に荷重が作用するため,砥石が破壊しないように,充分に気を付けて作業しなければならない。
ドレッシング条件
ドレッシングとは,研削砥石面にある砥粒を単石ダイヤモンド等で破砕して,切れ刃を生成することや目づまり面を除去することをいう。ドレッシングのことを「目立て、目直し」ともいう。
研削作業の特徴として, ドレッシング条件を変えることにより1枚の研削砥石で粗研削(荒研削)から精研削(仕上げ研削)まで行えるこ とが挙げられる。 粗研削の場合は,加工物の形状精度を良好にしつつ,能率よく取り代を除去できるような切れ刃を生成することであり,精研削の場合は精度よく表面粗さを整えるような切れ刃を生成することである。
そのためには,粗研削と精研削とでは,明確にドレッシング条件を変えなければならない。 ドレッシング条件は,その時の砥石面の目づまり, 目つぶれ,目こぼれ状態,並びにダイヤモンドドレッサの先端の摩耗状態によってわずかに異なり,それぞれの状態に対応して 作業者はドレッシング条件を少しづつ変えている。
ドレッサ切込み量であるが,切込み量が多いとドレッサの消耗が多くなったり,砥粒が 脱落して砥石面が損傷したりする。
通常,粗研削用ドレッサ切込み量および粗研削用ドレ ッサ切込み量は次のようである。
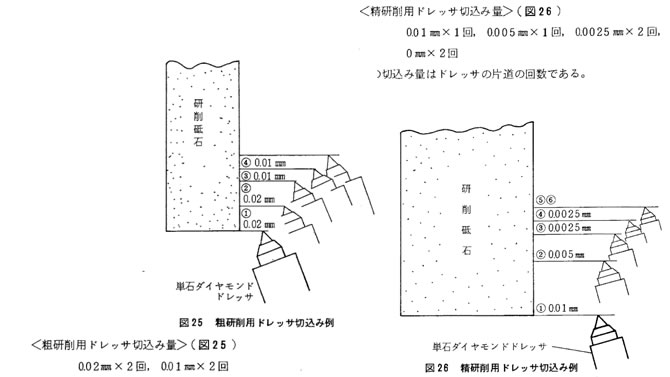
研削砥石ドレッシング量
研削条件
研削の場合には砥石全体にかかる研削抵抗と切れ刃である砥粒1個にかかる研削抵抗とを分けて考える必要がある。
ここでは,砥粒1個に作用する研削抵抗と研削条件の関係について考えてみることにする。
図30は,砥石切込み量 tを与えたときの砥粒の最大切込み深さt Maxを示している。
図において,真下にある砥粒1個の切削断面積は,砥石外周と砥粒の切削軌跡で狭まれた 斜線の領域である。
したがって,斜線部の最大厚みが砥粒の最大切込み深さt Maxでありt maxに比例して 砥粒1個にかかる研削抵抗が変化することになる。
今,砥粒の切削軌跡に着目すれば,砥石周速度,加工物速度(テーブル速度)および砥石切込み量によって, 切削軌跡が異なってくる。 そのためt maxが大きくなるのは,砥石周速度が遅い場合,加工物速度が速い場合および砥石切込み量が増大した場合であ る。
目こぼれが生じているような研削状態を「砥石が軟かく作用する」と言い,目つぶれや目づまりが生じているような研削状態を「砥石が 硬く作用している」と言う。
砥石周速度
砥石周速度は,研削抵抗と研削焼けとの関係、および砥石の遠心破壊強度との関連で決定される。
通常砥石軸の回転数は一定であるため,砥石周速度は砥石直径の大小で定まることになる。
平面研削における標準的な周速度は1200~1 8 0 0 m/minであるから作業時間とともにその直径が小さくなれば砥石周速度は低くなる。
砥石径が小さくなるとt maxが増大して目こぼれしやすくなり,砥石が軟かく作用するようになる。
したがって砥石径が元の2/3位になると通常使用されなくなる。
加工物速度
加工物速度(テープル速度)は油圧の流量制御などによって,調節することができる。
加工物速度は砥石周速度の1/100を目安としている。 加工物速度を速くした場合には,砥粒の最大切込み深さが大きくなって砥粒が脱落しやすくなり,砥石が軟かく作用する。
一方,加工物速度を遅くした場合には,加工物上で研削点での保持時間が長くなって研削焼けが生じやすくなる。
一般的に加工物速度を遅くした方が仕上げ面粗さがよくなるが砥石回転振れに起因する研削方向のうねりが目立つようになる場合がある。
また精研削過程では仕上げ面粗さを改善するために,加工物速度を遅くしたいところであるが,精研削用ドレッシングによって切れ刃が細かくなって研削焼けが生じやすくなっているため,加工物速度をそれ程,遅くすることができない。
したがって,精研削における加工物速度は粗研削の場合と同じか,あるいは粗研削の場合よりも幾分,遅い程度である。
砥石切込み量
砥粒が加工物に食い込んで切り屑を出す過程では,切削点での加工物の弾性変形で始まり,塑性変形へと進み,そして最終的に切削へと移行する。
さらに砥石と研削盤の弾性変形も加わるため,切込みハンドルの目盛通りに,砥石が切込んでいるとは限らない。
しかも,切れ刃の摩耗状態も異なるため,同じ目盛だけ切込んでも研削による火花の出方が 違ってくる。
このことを考慮して,規定の寸法に仕上げる必要がある。 砥石の切込みを増大させるとt maxが大きくなり,砥粒が脱落しやすくなるとともに,砥石と加工物の接触面積が増大して研削焼けが生じやすくなる。
また,砥石切込み量が増大すると,研削抵抗の増加により,加工変質層が増大し,研削による曲がりが加工物に発生するととにもなる。
逆に砥石の切込みを減少させると加工能率が低下する。 粗研削での取り代は6~120mmの厚み加工物で片側で0.1~0.2mm である。 精研削では,最終的な砥石切込み量は零で,仕上げるが,切込み量を段階的に少なくした方が,加工物の表面品質は向上する。
精研削の加工物の取り代は片側で0.01~0.02mmである。