旋盤
小物を対象とした 卓上型旋盤、 大型部品を対象としだ 立て旋盤、精密加工を目的とした超精密旋盤などがある。
一般に使用される旋盤が下図の普通旋盤 です。
旋盤では様々な形の切削が可能であるが,旋盤で削る動作を 総称して旋削と呼んでいる。
普通旋盤で行なう旋削の方法を (a)~(f)1こ示します。
(a)(b)は外面旋削(円筒削り)および内面旋削(中 ぐり)です。 回転する工作物に対し、工具に切込み(d)を与え,軸方向に送り(f)を与えれば,円筒面が切削加工できます。
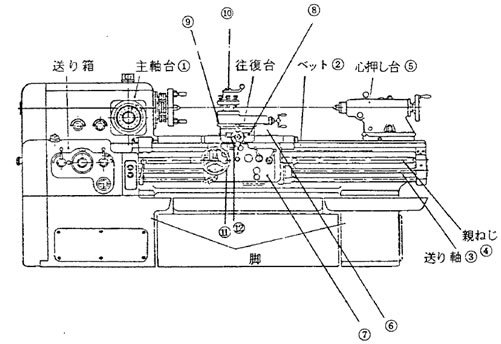
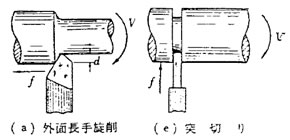

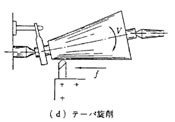
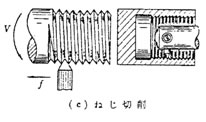
工作物を削るために保持する方式から分類すると下図のように工作物の片側だけを保持するチャック作業と 工作物の両側を支持するセンター作業に分けられます。
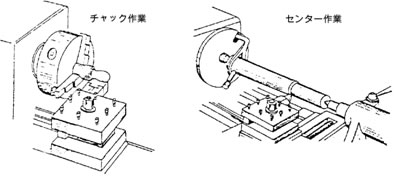
チャック作業で使用される物は下図のような取付け具が使用されます。
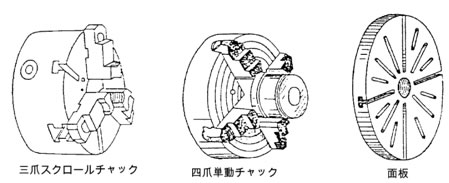
三爪スクロールチャックは端面に120°間隔で3つの爪があり 円周上の締付けねじを回すと3つの爪が同時に半径方向に移動できる構造で丸棒、六角材をを簡単に固定できるため、最も頻繁に使用される。
しかし、1つのねじで3つの爪を同 時に動かすので締付け力が分散されるのと、個々の差はあるが0.07mm位の偏心は避けられない。
1つの爪の変形や摩耗により 3つの爪の幾何学的対称性に誤差が出るので主軸の回転中心と工作物の軸心がずれるので、
軽切削であまり精度が必要ない工作物や 1回のチャックだけで
全加工が終了する ような工作物に対して用いられる。
四ツ爪単動チャックはチャック端面に4つの爪が90°間隔に配置され、円周部の締付けねじを回すことにより それに対応した爪だけが半径方向に移動できる。
4つの爪は独立した移動をする構造のため工作物の締付けカは強くなり 主軸の回転中心と工作物の軸心が爪の摩耗や傷に関係なく微調整できる。
円筒に限らず異形物の加工,重切削,加工精度の高い工作物などに用いられる。
四つ爪チャックの典型的な使用方法は、角材を削りだすことです。下記に要領を示します。
この応用で、任意の位置穴加工も可能になります。
面板は補助具を用いて異形物の部分的旋削に用いられる。 その他,チャックにはコレットチャック特定の太さの丸棒を効率よく高精度に加えるためのもので、おおよそ±0.05mm以内のものをくわえます。
油圧チャック、真空チャックなどがある。
バイト形状
ろう付けバイト標準形状番号
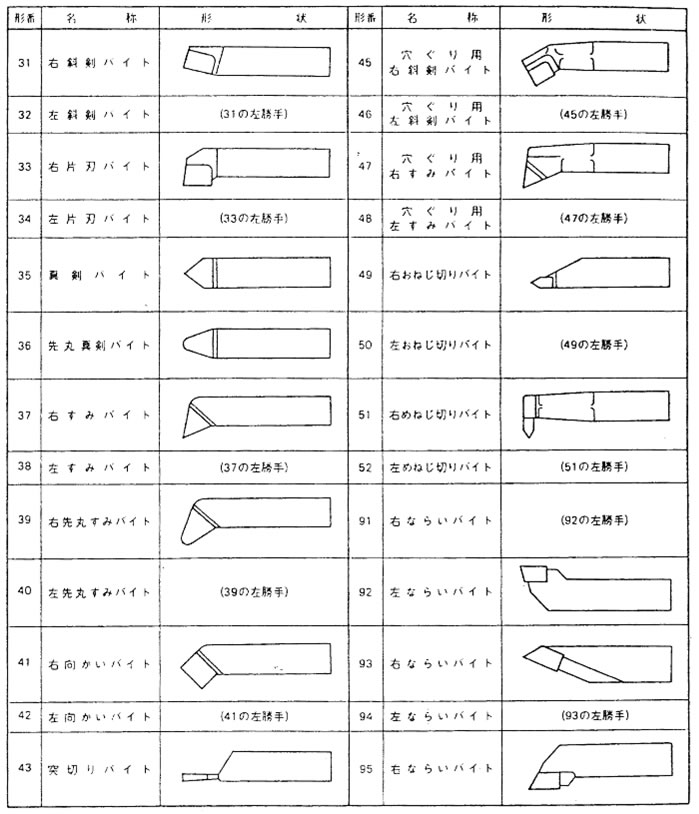
バイトの大きさ
超硬バイトには0-6番まで、7種類の呼び番号があり番号が大きくなるに従いバイトも大きくなります。
バイトの側面に31-3とかがあります。 これは31番の形状で3番の大きさのバイトということになります。 さらに細かく刃先形状を示すために以下のような表示方法が設定されています。
バイト刃先形状の表示方法
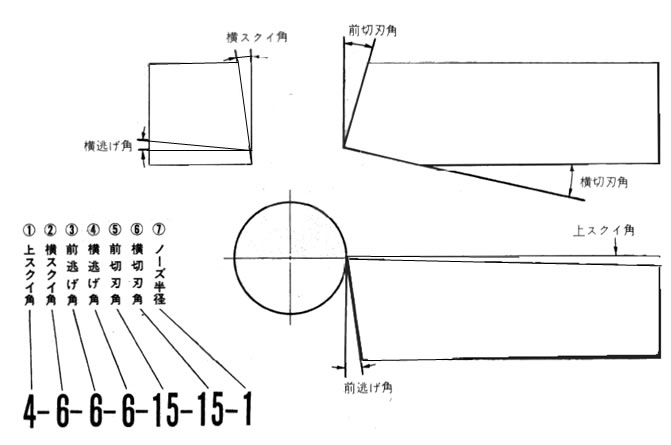
端面削り
円筒削りを行なう前に工作物の端面を削る作業を端面削りという。
端面削りの問題点は、主軸回転数が同じであれば外周部と回転中心付近で切削速度が極端に異なることです。
外周部は問題ないが中心付近では構成刃先が付着し、仕上面が悪くなり,超硬工具では切刃の欠損もあり得ます。
同一主軸回転数にせず 途中で回転数を変えるか 同一回転数の場合は外周部の切削速度を高めに設定します。
穴あき材料では下図(b)の切削送りもあります。
また端面の削り代が多い場合は(c)図のように片刃バイトによる円筒荒削りで代用すれば切削速度の変動が少なく能率的です。
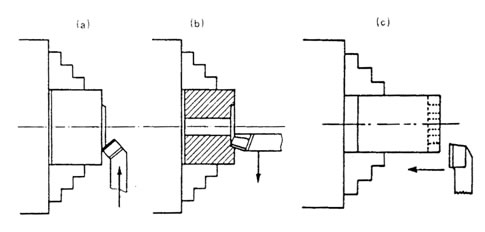
端面削りでは下図のように端面中心に削り残し(デベソ)ができることがあります。
この形状が円錐であれば刃先が高く、円筒形であれば刃先が低いことになります。
この部分の切削は切刃に無理な力が作用し 刃先欠損の心配があるので 刃先高さを回転中心に一致させ 工具刃先を回転中心より先へは絶対に進ませてはいけません。
センター穴あけ作業
チャック作業は工作物のチャックによる片持ち支持で加工するので 工作物の長さが直径と比較して長くなると切削力による曲げモーメントの増大、工作物のたわみなどにより 加工能率の低下ばかりでなく 安全性や振動発生などにより切削加工自体が不可能になります。
このようなとき工作物の先端中心にセンター穴をあけ 図50のように心押し台にセットしたセンターにより工作物を支持して旋削を行なう作業形式を片センター作業と言います。
安全性、,チャックの保持能力および加工能率の点からチャック作業と片セ ンター作業の作業形式の分岐点は工作物長さ(L)と工作物直径(D)の比で L/D=2 程度、また加工精度の点からは L/D = 3程度が1つの目安です。
両センター作業
回転軸など 工作物各部の回転中心が一致しなければならない工作物を加工するとき、三ツ爪チャックによる片センター作業ではチャック部分とその他の部分は同時加工ができず、また爪の変形などにより軸心を一致させることは不可能です。
また四ツ爪チャックによる片センター作業では、心出し作業を正確に行なえば軸心を一致させることは不可能ではないですが 作業者の心出し作業の負担が重くなります。
回転軸など工作物全体の回転軸中心を一致させる必要のある工作物の仕上加工 を容易に行なうため 両センター作業が使用されます。 下図に両センター作業を示します。
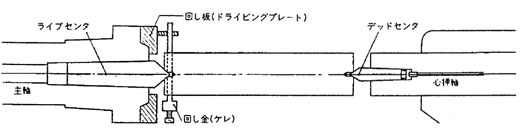
溝入れと突切り
溝入れ作業は右図のように工具を主軸回転軸に対し直角方向(横送り方向)に送る形式の切削で 円筒部に溝加工する作業であり 突切りは工具を工作物の回転中心まで送り込み 工作物を切断する作業です。
溝深さが浅ければ工具形状もあまり問題ありませんが 溝が深い場合および 突切る場合、外周切削工具と比較し 使用工具は特異な形状となり 切削作業も難かしくなります。
溝入れ作業と工具形状
溝入れ突切り工具の特徴の1つは切刃の突き出し長さが大きいことです。
下図に示すように溝入れ工具に主分力が作用したとき 工具は シャンク中心線の根元部分を中心として たわみ、切刃がシャンク中心線より上の位置にあるほど 切刃はたわみにより工作物に食い込むことになります。
たわみが大きいほど瞬間的に切削厚さが増.大し 大きな切削力が発生して振動発生のエネルギー源となると共に 場合によってはシャンクが折れることにもなります。
この危険を避けるため超硬工具では主切刃幅に対しシャン ク高さを可能な限り大きくし振動による切刃の欠損を防止しています。
ねじ切りの原理
旋盤作業で回転軸にねじを切る作業は多い。
旋盤には切削送り用の送り機構の他に 往復台は親ねじ送り機構によって送りをかけることができる。
円筒削りなどでは正確な送りは必要ないが ねじ加工ではねじのピッチ精度が問題となるため,ピッチの基準として親ねじ が使用される。
ねじ切りの原理を右図に示します。
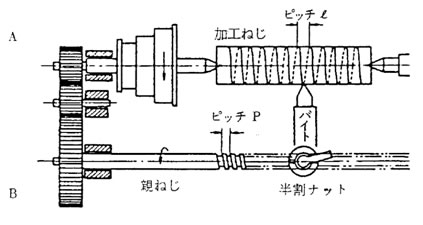
主軸に保持された工作物は歯車を介して親ねじと連結されていて、親ねじは 往復台のエプロンに設置されだ半割りのめねじ(ハーフナット)と噛み合わされ 親ねじの回転が刃物台の直線運動に変換されます。
親ねじのピッチをP ,加工され るねじのピッチを L としたとき主軸と親ねじを連結する歯車の比は 主軸側歯数をA、親ねじ側歯数をB とすれば L/P = A/B の関係を満足すれば目的のピッチ(L) を得ることができる。
加工されるねじのピッチにより上式の関係を満足するように主軸台の歯車列を変換する必要があります。
正確なねじを加工するには一回の切削だけでは切れないので複数回の 切削により仕上げざるを得ません。
.ねじ切り工具の形状
機械加工の原則は工具精度は二次的なものとして,工作機械の母型の精度を工作物に転写することです。
その意味で ねじ加工でのピッチは親ねじの母型精度を利用しています。
ねじ山の角度も原則として図(a)のよう に切削工具の送り運動で加工するのが理想です。 しかし加工対象となるねじ山の大きさが小さいときは運用として(b)図のように工具形状を 加工ねじの角度に合わせて成形し,工具切刃形状を工作物に転写する方法 が一般にです。
ねじ切り作業
加工されるねじの山角度はねじ切り工具の角度が転写されるので工具は右図のように工具切刃の角度をセンターゲージ などを用いて刃物台に正しくセットします。
工作物外径はねじ呼び径に仕上げるが、外径寸法は呼び径よりマイナス寸法にします。
また切刃の接触長さが長いのでセンター作業が可能であれぱセンター作業によるねじ切りが精度上望ましい。
中ぐり作業
外周円筒削りが円筒の外面を加工する作業であることに対し、中ぐりはボーリングとも呼ばれ 内面円筒削り作業である。
工作物に前加工されてなければ 下穴が無いのが普通である。
旋削用工具では下穴加工はできないので 下穴加工にはドリルが使用される。
中ぐり工具形状
中ぐりは下穴あけされた工作物の内径を目的の形状,寸法に仕上げる加工で す。
中ぐりバイトは 刃先が刃物台より相当長く突き出し 穴の直径によりシャンクの太さが制限されるので 外周切削と比較して加工能率、加工精度とも不利な加工になります。
右図に工作物と工具切刃および工具シャンクの相対関係を示す。工具切刃の心高は回転中心に一致させるのが基本である。
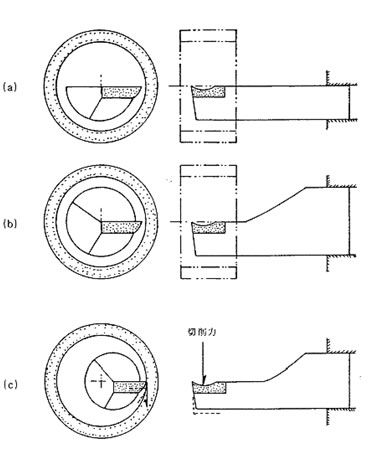
(a)図は外周削りと同様に切刃がシャンク上面に近い位置にある場合を示す。
(b)図は切刃位置をシャンク中心線に一致するようにしたもので同じ直径の穴加工を想定すると (b図の形式の工具シャンクは(a)図と比べ太くすることができる。
図(c)に示すように切削の主分力が作用したとき工具の突き出し長さが長いので、垂直変位も大きい。
このため切刃が降下したとき切刃の心高が回転中心にあれば工作物の曲率の関係で切刃が工作物に食い込むことになる。
外周切削ではヘール形式の工具で対応できたが中ぐりではこれは使用できないので中ぐりの心高は回転中心より高めにセットするとよい。 また作用逃げ角も曲率の関係で減少するので前逃げ角は穴径により工夫する必要がある。
中ぐり作業の3通りの切削形態を下図に示す。
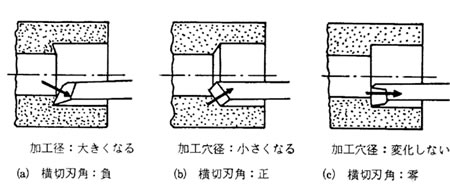
中ぐりバイトの横切刃、前切刃およびノーズ半径の役割は外周切削工具のそれとまったく同じである。
ただ突き出し長さの配慮を加味して対応すればよい。
図(a) は横切刃角を大きな負角にしたもので 段付き穴やめくら穴の隅を加工するのに便利である。
図中の矢印は送り分力と背分力の合成力を表現したもので横切刃角が大きな負角であると 合成力は切刃が工作物に食い込む方向に働き、穴径が加工予定寸法より大きくなる。
(b)図は斜剣バイト形式で 刃先強度があるので荒加工に適すが 合成力が工具と工作物を離す方向に 作用し 加工穴径は予定より小さくなる。
(c)図は片刃バイト形式で 実際は横切刃角を少し負角にし,ノーズ半径による背分力と送り分力の合成力方向を軸方向と一致 させた工具である。
この状態では工具変位は主分力による垂直変位だけなので 穴径の変化は少なくなる。
中ぐり工具の周囲は工作物なので切りくず排出条件は外周削りより悪くなる。 工具シャンクを加工穴径と同程度に太くすると切りくず排出に必要な空間が無くなるので 荒削りでは適当な空間が必要である。